Sodium chlorate is an amazing compound that, when burned, creates plentiful oxygen. This chemical reaction is relied upon in airplanes, submarines, and space stations as a backup source of oxygen. Learn how MPE Gran-U-Lizers and MPE Systems Group are behind the processing of this product for a major aviation supplier.
Aerospace companies, navies, and space agencies keep backup oxygen generators onboard their craft in case of a loss of cabin pressure or a shutdown of primary oxygen generators. These backup oxygen generators, usually in canister form, require no electricity to operate and can produce a consistent amount of oxygen for extended periods. The chemical inside the canisters is sodium chlorate (NaClO3). The byproducts of the reaction are table salt (NaCl) and pure oxygen. The reaction is also exothermic; hence referred to as burning. In order to promote a consistent burn, manufactures need a narrow and uniform particle size distribution of the sodium chlorate. Additionally, because these devices are important for the safety of human lives, aerospace companies want a system that stores important batch and quality control information for testing and tracking.
Examples in Aviation and Submarines
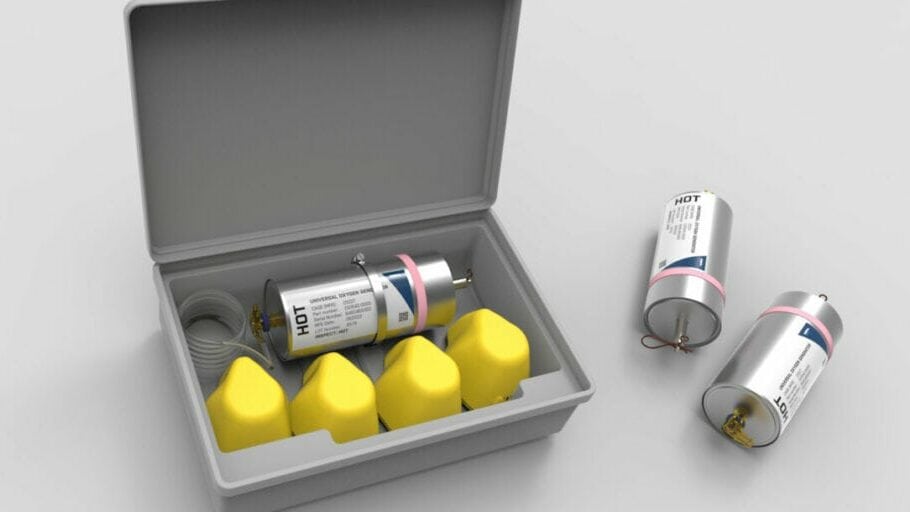
System Specifications
A major supplier of emergency oxygen canisters contacted MPE for supplying a complete process system that achieves the following specifications:
- An exacting particle size output with no overs, and minimal fines as per customer specifications
- Automated dumping and automated bagging with dust collection, as well as data capture with process timestamps
- Safe, low-noise and dustless work environment that one employee can easily operate
MPE Systems Group engineered the process system with the following equipment:
- Automated dumping station
- Delumping grinder
- Overs screener for particles in excess of 3mm
- Vacuum pneumatic transport
- IMD 79 Gran-U-Lizer for precision grinding of sodium chlorate
- Check screener for particles in excess of 1mm
- Dust collection
- Finished product drum filling and weighing
- Complete PLC integration for seemless operation
The System in Action
Results
The system excelled in all FAT testing and is currently installed onsite at the customer’s facility. The manufacturer is able to track batches with all grinding parameters saved. For more information on the MPE’s precision particle size reduction technology paired with its complete process systems capabilities, reach out to MPE at 773-254-3929 or solution@mpechicago.com.