Ferris Coffee & Nut Co. is a specialty roaster located in Grand Rapids, MI. They first reached out to MPE with the goal of modernizing their previous operations to achieve a higher level of food certification required by their wholesale customers as well as increase their capacity, efficiency, and beauty of their coffee operation.
Ferris’ needs
- A complete green coffee cleaning system with dust collection
- A green bean silo storage with recipe driven control system to automatically deliver batches to two 120 kg batch roasters
- Water-cooled grinders for increased ground coffee taste and aroma retention
- Tubular drag Chain-Vey conveyor implementation throughout the facility to move all coffee (green, whole bean, and ground) while keeping the coffee enclosed
- A Plant Control System to coordinate all coffee movement—from unloading green coffee to final packaging
MPE’s solution
- An unloading mezzanine and bean cleaner
- Four 7500 lb capacity storage silos
- A 700FX grinder
- A 600FX grinder
- Packaging surge hoppers with dust collector
- Six 4” tubular drag Chain-Vey conveyors.
- Implementing PLC controls that allowed the system to be as automated or manual as desired
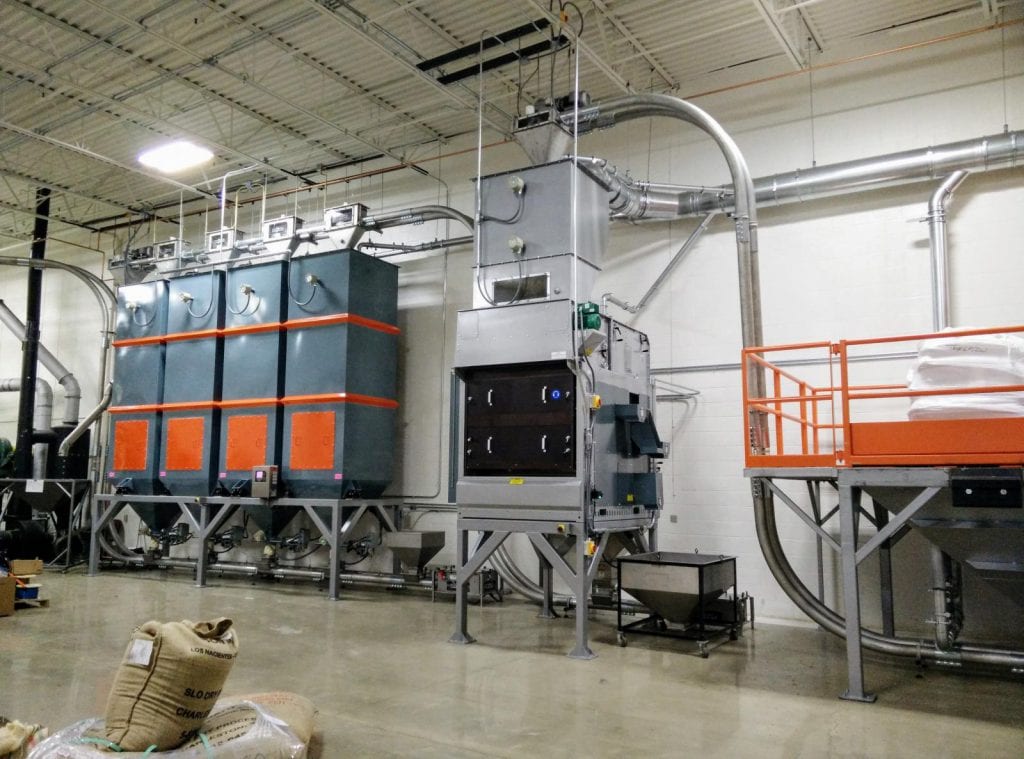
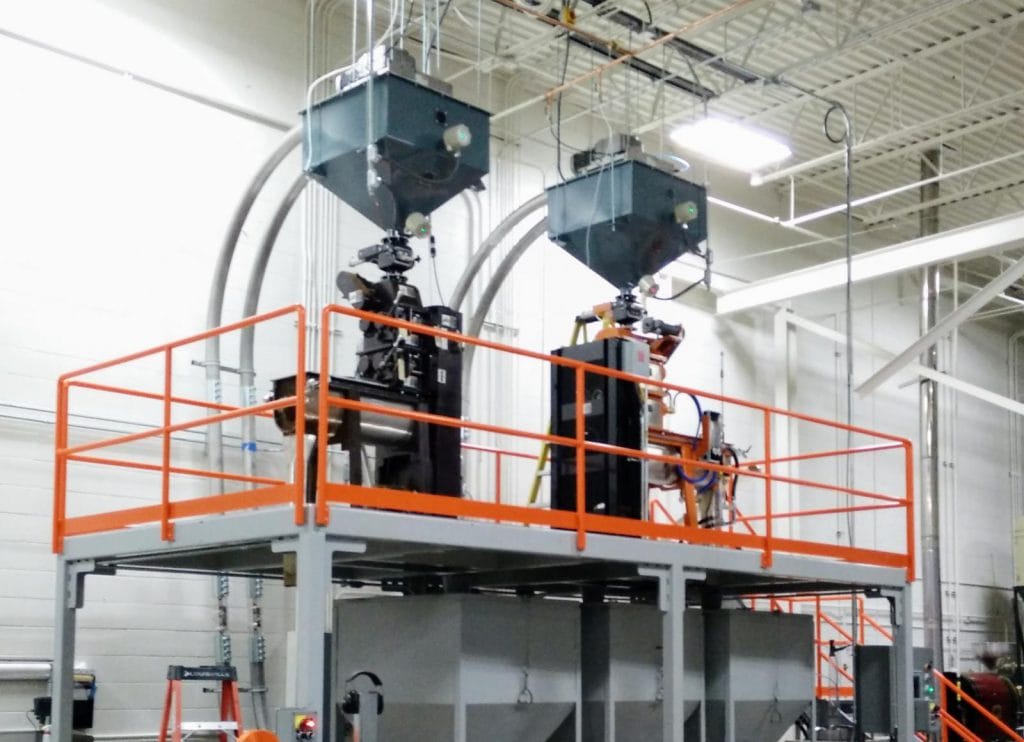
The value for Ferris utilizing MPE’s grinders, Chain-Veys, and process systems integration has been tremendous in terms of efficiency and flexibility.
“With the installation of the new system, we’ve managed to meet all the needs that drove the project in the first place,” noted Sam Mirto, Director of Coffee at Ferris.
The original goal of meeting a customer’s auditors’ exceptional food safety standards was achieved. Other savings have resulted from more efficient use of labor. With the implementation of advanced process automation, one person can be grinding coffee and packing thousands of pounds of coffee seamlessly, whereas previously these were separate tasks that required multiple employees before the renovation. This efficiency also positions Ferris to accommodate increasingly large customers with ease.
Another benefit of the beautiful open layout and design of Ferris’ build-out is the pride of touring the facility to potential customers. With the implementation of Chain-Vey’s clear tubing, people can follow the coffee along the production process and walk away with a deeper understanding of the operation.