Leading equipment provider modern process equipment offers a glimpse at the future of coffee capsule manufacturing.
When coffee capsule technology was first introduced in the United States, few could have anticipated the impressive impact those little pods would eventually have on the coffee industry.
Dan Ephraim, President of Modern Process Equipment (MPE), remembers when one of his clients first patented the technology over 15 years ago. With coffee pods (also known as soft pods or pads) – the predecessor to the capsule – never quite taking off in the United States, he says the commercial potential seemed limited in a market not accustomed to single-serve.
“At the time, the difference between capsule and pod technology was not all that apparent,” says Ephraim. “Both were single-serve systems that were painted with the same brush.”
Fast-forward a decade and a half, and those companies who saw the potential for capsule technology have seen their foresight pay off. US market leader Green Mountain Coffee Roasters attributed 90 per cent of its US$3.9 billion in net sales to Keurig brewing systems, accessories and single K-Cup packs. European leader Nespresso is now present in more than 60 countries around the world, with 180,000 unique customers visiting its online shop daily.
MPE’s Scott Will says that the key to the success of capsules over pods has been the ability to deliver quality in the cup. “A decade ago, when you went to make a coffee with a pod it wasn’t exceptional,” says Will. “I remember the first time I tried Kona coffee in a capsule, and it was so amazing – the flavors really came through. The ability of the capsule to deliver that quality definitely had something to do with its success in North America.”
Ephraim points to pods’ limitations in the paper filters’ impact on the quality of the brewed coffee. “With the pod, you have water going through the filter on both sides. This makes the coffee taste different,” he says. “The capsule is just like brewing a fresh pot of coffee. You can control the elements around the brew chamber. If you can technically iron out all those challenges, then you can make a good cup of coffee.”
Like any overnight success, Ephraim says it took a while for this technology to “work itself out” before it took off in the US. It’s this foundation in quality that is now serving as the basis for the future development of coffee capsules in the US, and indeed around the world. As pioneers in developing the equipment for the first coffee capsules, MPE is well-placed to be leading the technological forefront.
From a manufacturing perspective, when MPE was first approached to assist with the production of coffee capsules in the US, perfecting the grind was a central focus of technological development. Ephraim explains that the performance-based grind for coffee capsules is quite technical. Similar to the parameters that baristas use on an espresso machine, the uniformity and particle size of the grind must be highly accurate to produce a quality cup.
From a manufacturing perspective, the grind is even more critical in ensuring factory operations are running at maximum capacity. “We’ve seen factories increase their capacity from 200 units a minute to 800,” says Ephraim. “At those rates, the need to fill each capsule accurately, with a specific amount of coffee, is critical.” To address this need, MPE has added normalization and densification elements to its grinders. The densification elements standardize the amount of coffee in each capsule, while also increasing the density to ensure the coffee fits into the pods.
The ability to control these two elements becomes paramount when considering that the coffee used will never be a constant factor. From different origins to roast methods, the physical characteristics of coffee vary constantly. MPE’s developments have focused on how to control these factors, while increasing a plant’s manufacturing capacity.
In the process, MPE has developed the MPE Vortex Super Homogeniser. The Vortex can increase density levels to twice the previously achievable range. The breakthrough configuration optimizes densifier speeds for specific coffees and density levels, allowing for precise density control of both high and low density coffees on a single machine. “That’s been a revolutionary design,” says Ephraim. “The ability to put an accurate amount of coffee in a capsule, and virtually any quantity without an elevation in weight and product over flow.”
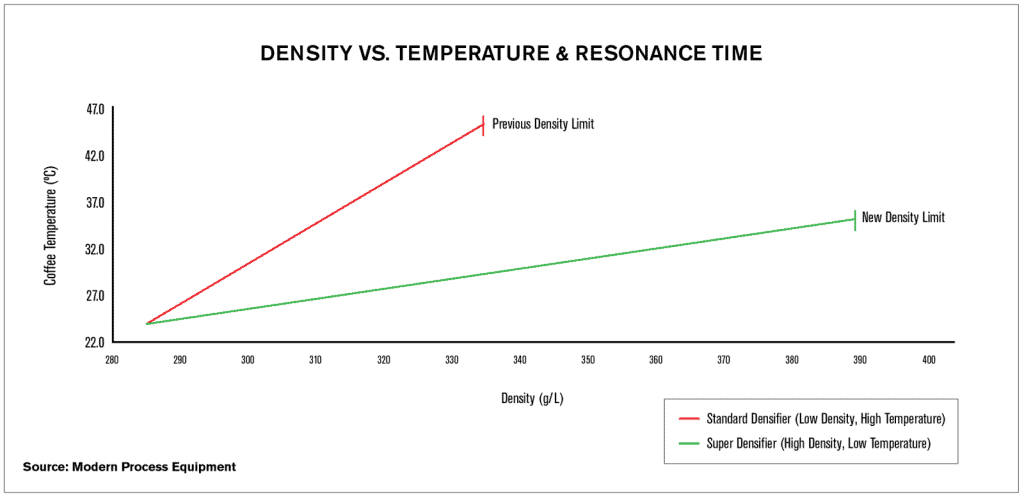
Important in the quality equation, is that the Vortex works with less than half the temperature rise of the coffee in the process. Because aromas are released as coffee is heated, Will explains that minimizing temperature rises has been a key focus in the development of the Vortex. The equipment features water-cooling of all the elements of the grinder – from the rolls to the normalizer – all on a PLC controllable system.
“As part of the initial design, we’ve been looking at keeping coffee colder and colder,” he says. “We’re seeing less of those volatile aromas lost between the grinding and packaging process. We can maintain the temperature and keep it cool during the densification process.”
From a sustainability perspective, the Vortex works with half the energy consumption of comparable previous products. Some of the inspiration for the Vortex came from MPE’s work in Europe, with espresso capsules more popular across the Atlantic. “We were working with some of the biggest capsule manufacturers at the time, who turned to us for our ability to produce higher density,” says Will. “It really opened up our eyes to what was happening in Europe.”
As the espresso capsules are a much smaller capsule size than what is standard in the US, MPE’s expertise in increasing density has come in handy. Because the amount of coffee that can t in a small capsule size is limited, the only way to increase brew strength is to increase the density of the coffee. MPE’s Vortex technology allows clients to increase that density without altering the particle size of the grind.
This is where Will and Ephraim see the future of coffee capsules, where a company with Vortex technology will be able to set its products apart.