Cool Beans Canning Co. is a large consumer canned beans food company producing high-quality products in their Minnesota facility. Their product range encompasses nearly all varieties of popular beans such as lima, black, navy, red, kidney, and garbanzo. Cool Bean’s largest competitors are other large national and private label brands; and despite a competitive business environment they have enjoyed increasing consumer demand for their products. By mid-2017, they opened a new 589,000 square foot facility to keep up with production needs.
Cool Bean’s Needs
For Cool Beans, one of the most important operations is the unloading and storage system for the dry beans when they arrive to the facility. They needed a conveyor system that could handle product bulk densities of 50 pounds per cubic foot and move dry beans at a rate of 70,000 pounds per hour. Plant managers wanted 12 storage silos, each with enough capacity for about one and a half truckloads of dry beans. Then transport the beans from the silos to an array of hydration and canning process systems.
MPE’s Solution
MPE designed a process system with the following:
- Two truck unloading conveyors moving product vertically for silo loading
- Two silo loading conveyors transporting product horizontally to twelve discharge points
- Twelve silos for intermediate storage
- Six silo unloading conveyors moving product to blancher loading conveyors
- Three blancher loading conveyors which transport product upward to introduction into the blanching process system
- One bulk bag loading conveyor for handling of specialty product not intended for silo storage
Truck Unloading
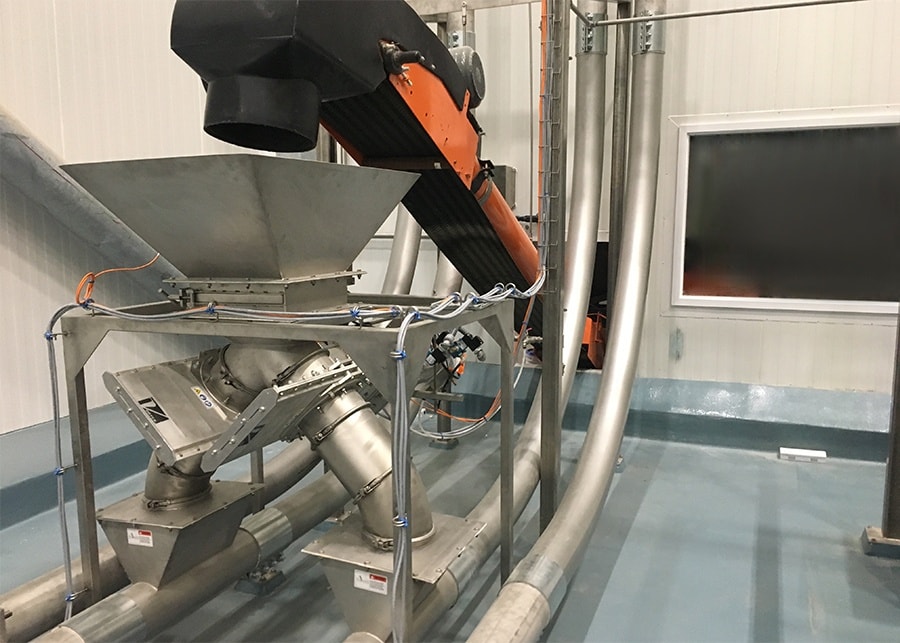
45 Foot Vertical at 50 lb/ft3
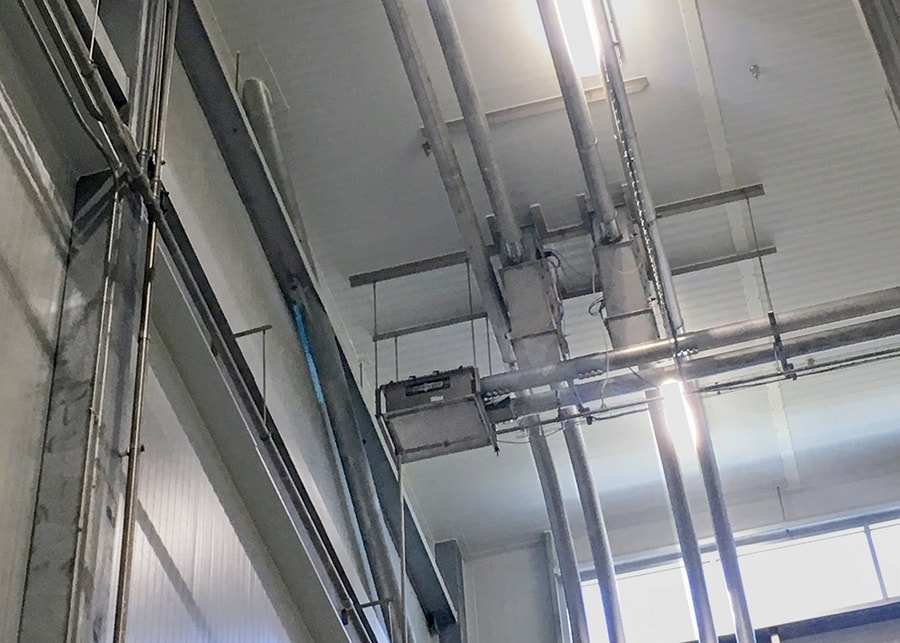
Let Down System
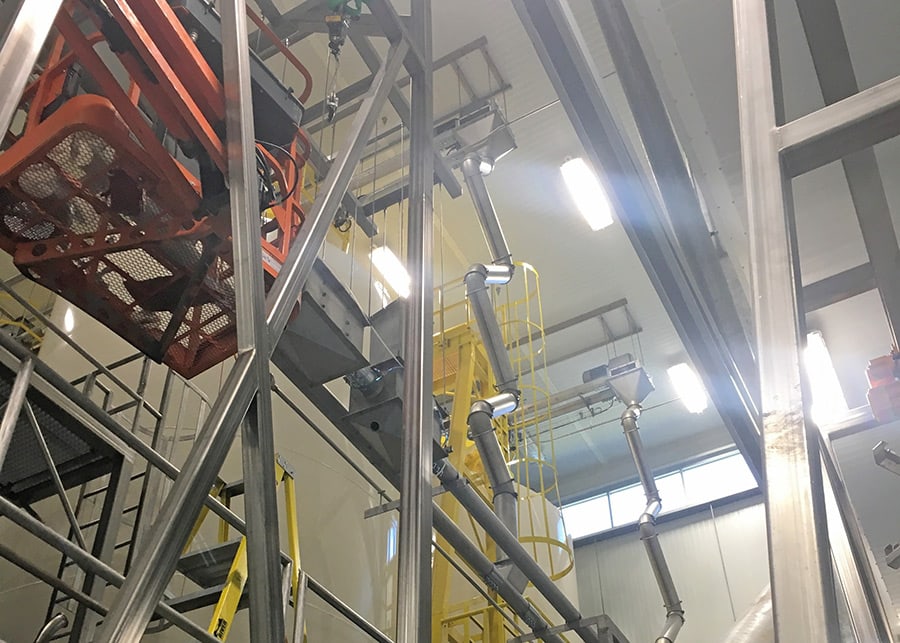
Under the Silos
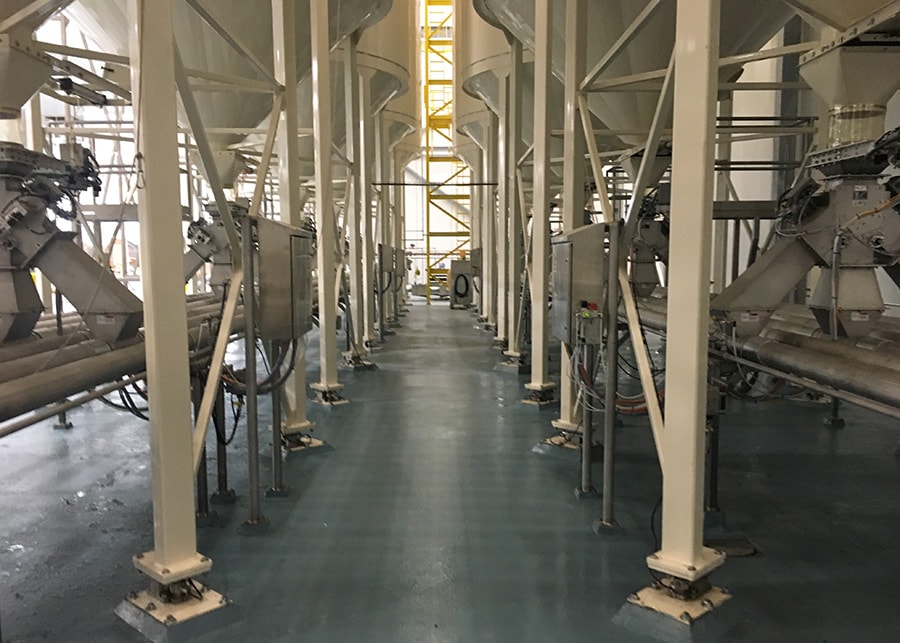
Blancher Loading Conveyor
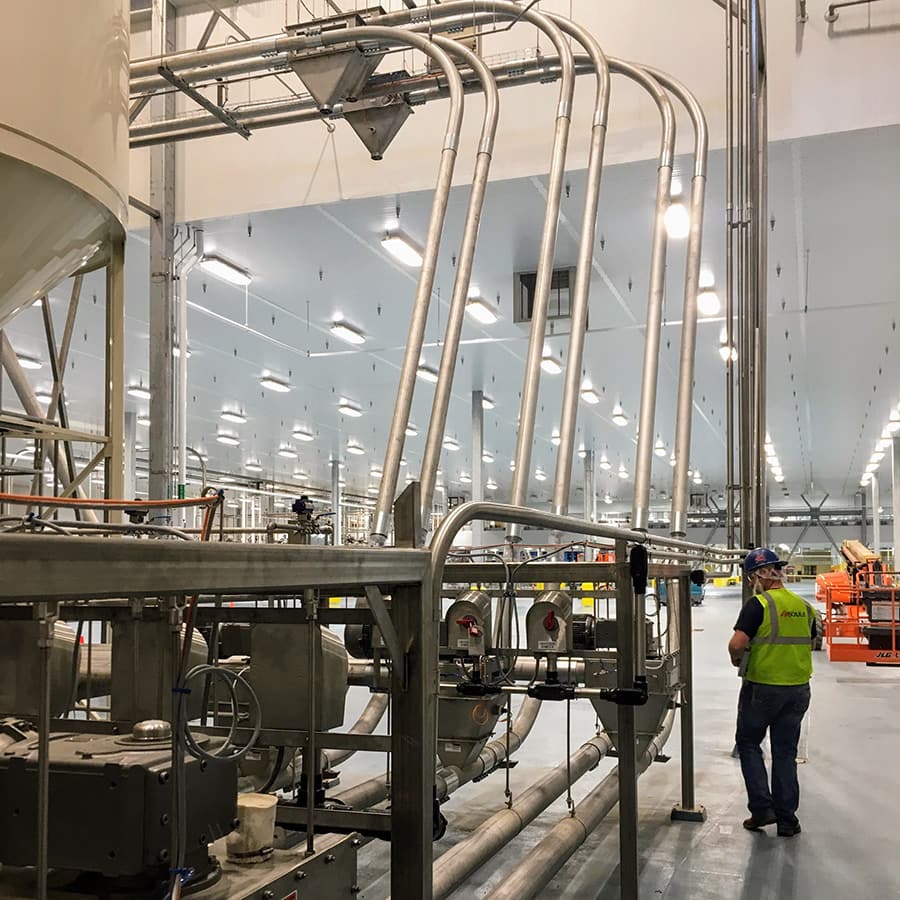