Understanding how various conveyors impact your product during processing is a critical part of equipment selection. While there is no shortage of conveyance options for dry processing and bulk solids handling, making the right choice for your products is not always straight forward. One of the paramount questions is: What effect will each of these conveyors have on my product’s composition? From this paradigm, the conveyor you thought was a great value or one you had the most familiarity with, suddenly is far from ideal and not the right choice.
Less than Optimal Conveyors Can Degrade Bulk Solids
Unlike grinding or mixing operations, which intentionally alter product composition as a value-add operation, incorrect bulk solid conveyance can unintentionally degrade the product and adversely impact the product quality and, therefore, overall process efficiency.
For coarse bulk solids, i.e., anything larger than 1/4 in, the impact of conveyance on the product is often visible and easily measured. Categorized as a type of degradation, breakage, affects products such as Beans, Seeds, Cereals, Snacks, Kibble, etc. Producers of these products can set shape and size specifications, and aesthetics, to be maintained throughout processing. Anything outside of the set spec is removed from the product stream. For obvious reasons, producers go to great lengths to prevent breakage. Chain-Vey, a tubular drag conveyor, is a natural choice due to its gentle conveyance capabilities. (Reach out to a Sales Engineer to do testing on your product that includes a full Breakage Analysis).
How Bulk Solids Interact with Conveyor Systems
As bulk solid particles get smaller or more varied (i.e., batch mixes), the impact of conveyance on the product is difficult to see visually. It can have a more significant impact or downstream processes or final product quality. Categorized as the second type of degradation, segregation, or declassification, affects products such as baking mixes, fine ingredients/flours, and chemical powders that must maintain a specific particle size, density, and composition throughout processing. Any small variances in particle size, density, or distribution can cause issues regarding overall product quality or process efficiency. Unfortunately, granular materials segregate by nature. Different sized, particles, and shapes all have individual flow characteristics and react to forces differently. Depending on how a conveyor applies a force to move the particles, segregation can be introduced during conveyance.
Take your morning cup of coffee, for example. Ground coffee is not truly a uniform batch of particles. It is a collection of particles of varying sizes. Furthermore, depending on the style of coffee (e.g., espresso, filter, or K-Cup), the grind/particle profile varies. Once ground to the right spec, the coffee then needs to be transported to intermediate storage and/or packaging.
The Negative Impact Using the Wrong Conveyor System
Unfortunately, if the wrong type of conveyor is used, the time spent fine-tuning the grinder is all for nothing as the means of conveyance segregates or further works the product after grinding.
If pneumatically conveyed, the ground coffee will travel at different velocities based on particle size and mass. The resulting product that exits a pneumatic conveyor’s discharge is no longer like it was when it entered the conveyor. Instead, the coffee is segregated with the lightest particles coming out first, and the heavier particles last, distorting the proportions of the final product impacting brew quality and customer satisfaction.
While segregation can be reduced through the use of mechanical conveyors, selection must still be thoughtfully considered. A screw conveyor, for example, achieves less segregation than an air system, however, the tumbling action of the product as it moves through the conveyor results in some measurable declassification of the varying particle sizes.
Unlike pneumatic systems and screw conveyors, which can result in conveyance induced segregation, the Chain-Vey is a mass flow conveyor in which all particles are in motion at the same speed and position. The gentle conveyance of the Chain-Vey facilitates a first in – first out the transfer, maintaining particle size and distribution within each pocket.
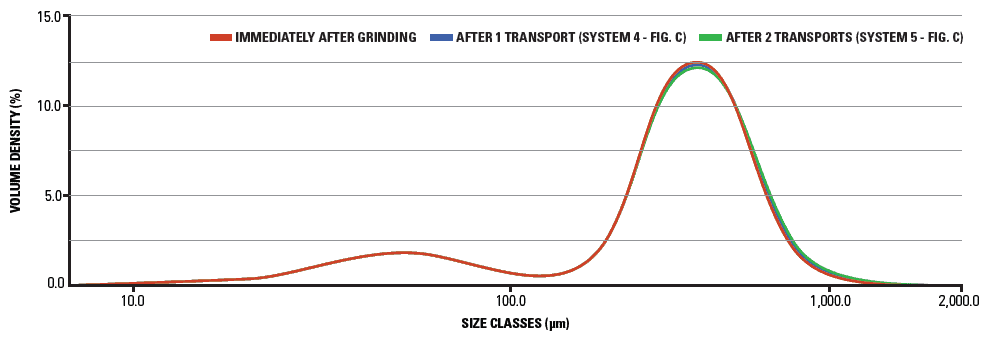
Figure 2: Ground Coffee Particle Integrity After Chain-Vey Conveyance (2)
In addition to preventing segregation, only tubular drag conveyors offer additional benefits which make conveyance selection easy:
- Fully enclosed design
- Dust-tight, environmentally sealed design
- Fully automatic, self-cleaning
- Flexible, multiple-inlet and discharge design
- Low energy, quiet operation
- Bi-directional operation
In closing, moving a bulk solid so that it does not lose its mixed homogeneity during transport can be critical to overall process efficiency and product quality. While some conveyance alternatives may be able to move the product physically, they may simultaneously introduce product segregation.
With the entire array of benefits, Chain-Vey tubular drag conveyors are the best choice for transporting applications where absolute minimal declassification is paramount. Speak to a Chain-Vey sales engineer today to learn more.