A Green Approach to Transporting Dry Products
In any processing or manufacturing facility, the transportation or conveying of products is a key element in the process. Conveying is not generally considered a process in itself, but is rather the link that connects other processes such as blending, grinding and packaging. In this regard, while maintaining the product integrity, grind size and consistency.
For instance, let’s take a product like cashews. It is vital that the conveying system neither damage nor break apart the whole cashews as they are transported from one location to another. Ordinarily, with a screw, pneumatic conveyor or other type of conveyor, there might be unacceptable amount of breakage; conversely with the Chain-Vey™, the whole cashews are transported with no compromise in quality. The amount of breakage evident in the final package is just one of the quality points of the Chain-Vey™.
Another, and possibly the most important, element of the conveying process concerns the transportation of ground products, wherein the particle size integrity and sample consistency, which is a function of particle segregation (declassification), is critical.
For instance, when dry products are ground, the resultant partial distribution is made-up of a number of different partial sizes, which constitutes the “profile.” Shown as the blue line in Exhibit 1, this ro-tap result illustrates the actual grind exiting at the grinder.
Particles are retained at the specific percentages on each of the screen sizes. The key is to ensure that the grind profile going into the final package has exactly the same grind, or particle distribution, as that which was discharged at the grinder. This sounds a lot simpler than it is.
With this in mind, if a transport system that is not specifically designed for maintaining grind integrity is utilized, the particle, distribution after conveying might appear like the pink line in Exhibit 1.
This is a huge problem and solutions in the industry have ranged over the years from bucket, screw, drag, dilute, and dense phase pneumatic conveying systems. Each system has strengths and weaknesses; but there is no question that a void has existed in the marketplace for a conveying system that can move particles, large or small, great distances without product degradation.
For this reason, MPE developed the Chain-Vey™, a tubular drag chain system that utilizes a 316 stainless steel chain to gently move materials utilizing molded food-grade “pucks” that are pulled by the chain through a stainless steel tube (see Exhibits 2A &2B). The result is an extremely energy efficient system that protects the products from damage, declassification and segregation.
As a point of reference, the Chain-Vey™ almost acts like a bucket elevator, gently carrying segments of product from one location to another. More specifically however, Chain-Vey™ offers a number of advantages including:
• Very flexible, multi-directional design capability
• Long distance,, closed conveying (100 meters)
• Multiple inlets and discharge points
• Few moving parts and low maintenance
• Energy efficient
Typical Chain-Vey™ Configuration
In both of the [below] cases (Exhibit 3, Exhibit 4), the product moves gently through the Chain-Vey™ through the use of “pucks” that are molded on the stainless steel chain. This chain is extremely durable, and will not stretch, fray or deteriorate in any other manner.
Turns or corners, in the system are accommodated through the use of “sweeps” that can range from 10- to 90-degrees and are designed to minimize friction. When necessary, “live corners” with rotating wheels that eliminate friction, are utilized enabling long runs and multiple run situations.
Chain-Vey™ as a Green Alternative
Typical power requirements for the Chain-Vey™ range from 1- to 50 horsepower and, when compared to alternative conveying systems, as a dilute- or dense-phase pneumatic systems, the energy savings can be as much as 90-percent. Assume that the requirement exists for 100-foot conveyor length at a run rage of 12 hours-per-day and 250 days-per-year.
Summarizing, MPE’s development of the Chain-Vey™ conveyor technology meets the increasingly challenging demands of bulk product transport in a flexible, efficient, and green alternative to traditional conveying methods.
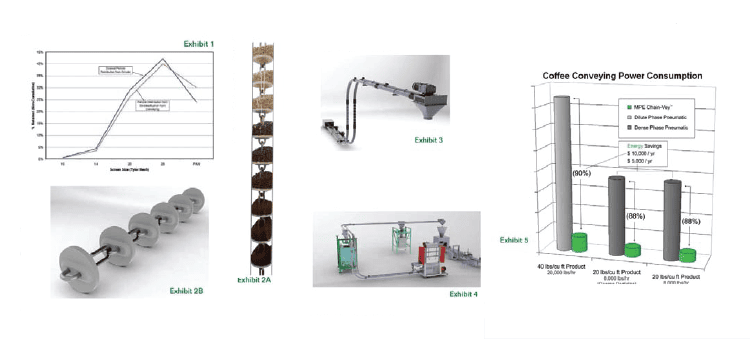