A large scale salt processor in the Middle East reached out to MPE, partly based on MPE’s valued role in a large US-based salt grinding operation, to assist them in their own efforts to scale their grinding operation.
The company’s Himalayan pink salt is a globally exported favorite, used by many at-home cooks and professional chefs. They import large feedstock, or salt chunks, which are then processed into mean particle sizes from 0.5 to 1 mm. The rate of production is around 8,000 Kg/Hr at this installation, however some models of MPE grinders could reach up to 10,000 Kg/Hr of throughput.
Original Feedstock Size
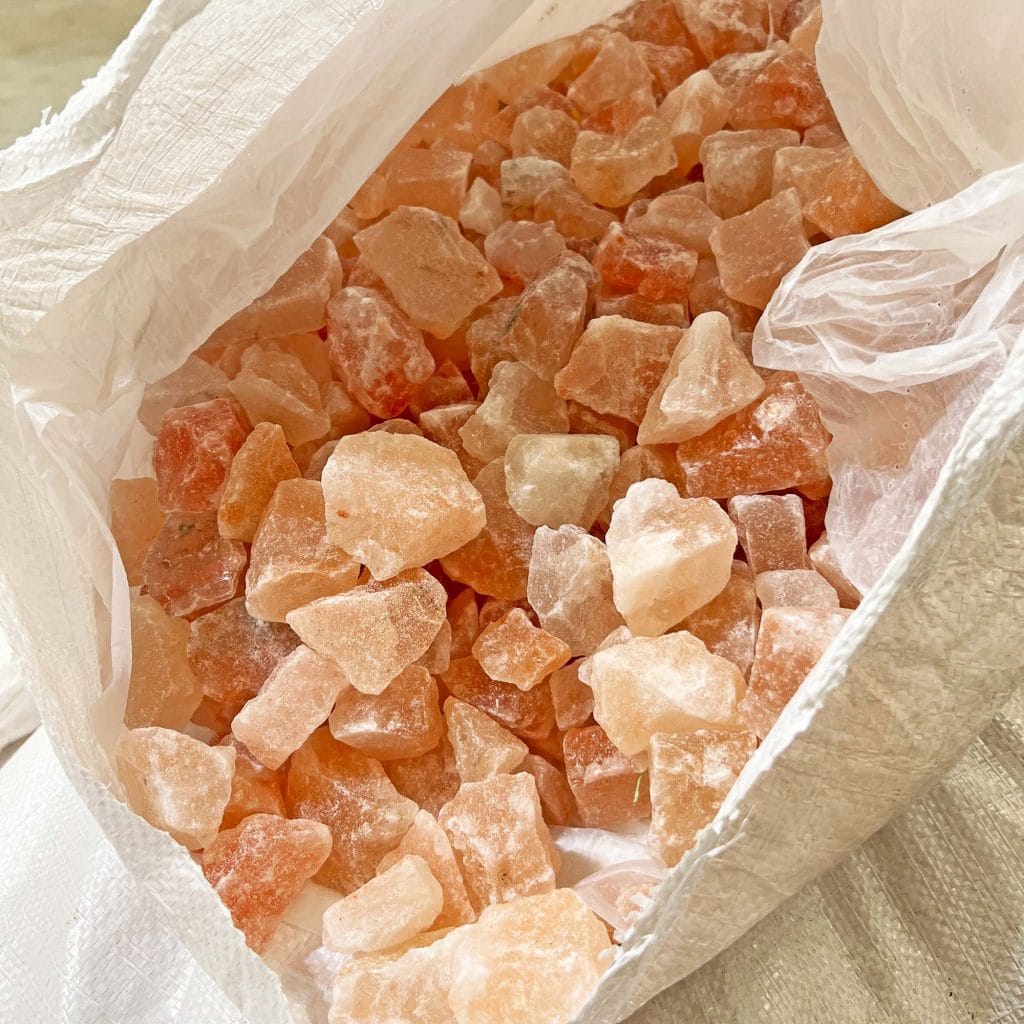
The incoming feedstock are large chunks, some as large as 10 cm in diameter. They first need to be pre-crushed into smaller feedstock using a hammer mill, which breaks them down to 2-3 cm in size.
First Pass into a 3 Section IMD 1052
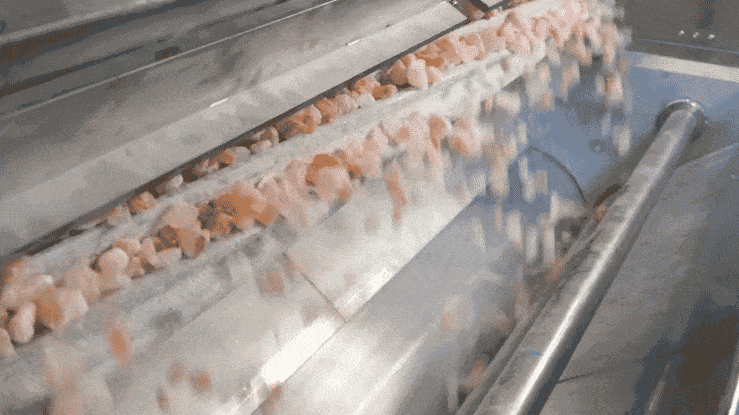
Details on the 3 Section IMD 1052
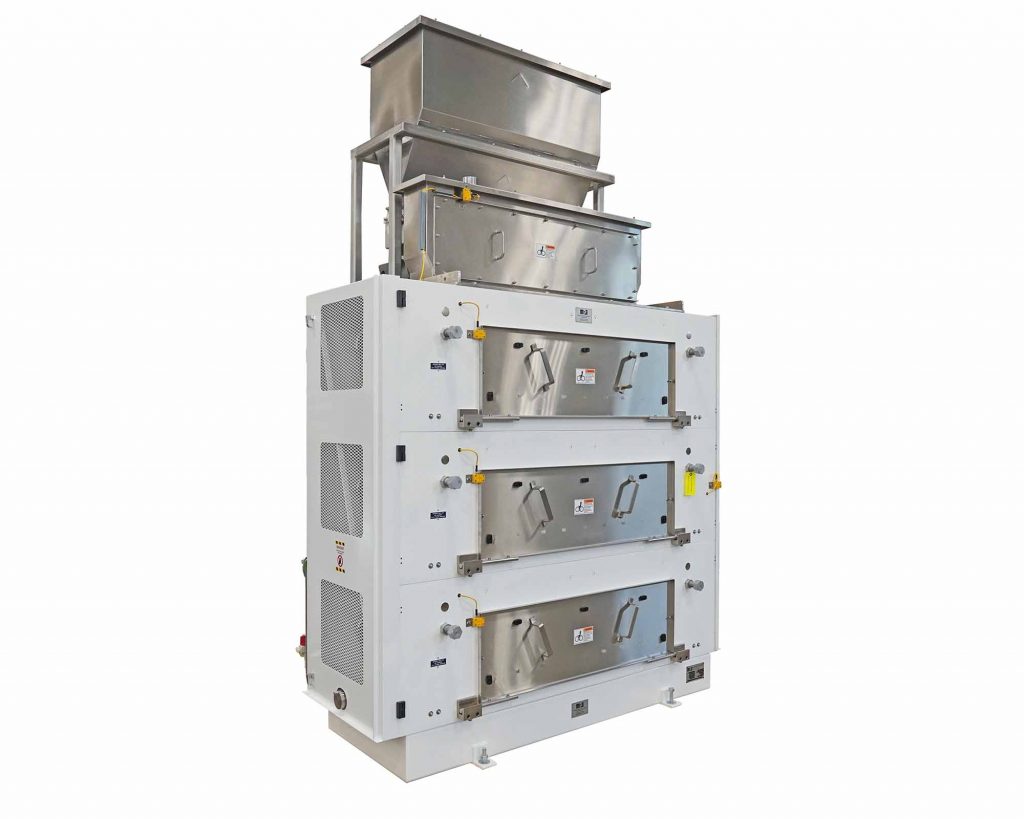
- 8,000 Kg/Hr consistent throughput
- Feedstock size: 2-3 cm chunks of salt
- Pneumatic roll gap adjustment
- Automated, adjustable, repeatable grind specs when switching between settings
- Electroless nickel plating on interior surfaces
Sorting and Additional Processing
After passing through the first grinder, the salt flows through a large vibratory screener. This screener sorts the salt into three product streams based on particle size:
- >6 mm in size, which are diverted back to the first 3-section IMD Gran-U-Lizer.
- 4-6 mm in size, which are diverted to a 2-section IMD 1052
- 1-4 mm in size, which are diverted to another 2-section IMD 1052
Two Section IMD 1052 Up Close
There are (2) discrete 2-section IMD 1052 Gran-U-Lizers that intake various larger-than-spec sized product for further processing. Depending on the final target product size, the roll gaps of each grinder will adjust to meet the target specification. Typically though, one grinder will intake product between 4 to 6 mm, while another grinder will intake product from 1 to 4 mm. A typical final target particle size is between 0.5 to 1 mm, or even smaller. Additional vibratory screeners, screw conveyors, and controls automation are part of this process flow.
Results
The (3) MPE IMD 1052 Gran-U-Lizers exceed specifications. They deliver on the targeted particle size reduction. MPE is also able to offer timely regional support with its global network of offices and representation if needed. During commissioning, an MPE sales engineer was on-site, bringing expertise on size reduction and training plant staff on maintenance of their world-class Gran-U-Lizers.
A large factor to MPE’s success in its role in this project is the thorough validation testing done before the grinder is build, and again after its completion. The laboratory results model real world usage; ensuring the the rate and target particle size objectives are met before shipping. This video below shows the testing of one machine before shipping.
Contact MPE at [email protected] or +1-773-254-3929 to learn more about precision particle size reduction equipment or our complete process solutions for dry foods. To learn more about Himalayan pink salt, read this article on interesting facts.